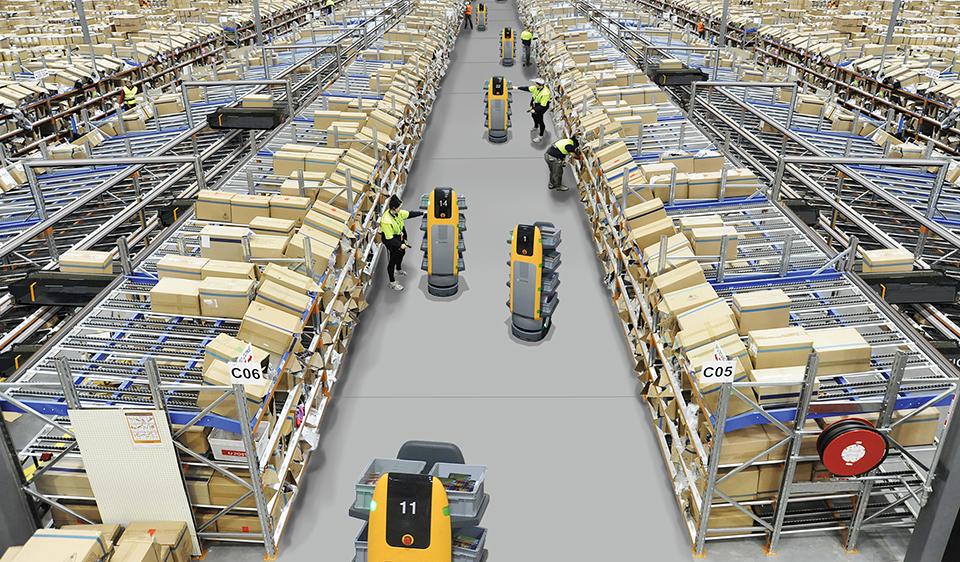
Autonomous vehicles are transforming warehouse logistics.
Dematic
Elon Musk may be the one bringing self-driving cars and trucks into the mainstream, but autonomous vehicles are old news for the manufacturing and logistics industries.
Driverless forklifts have been roaming warehouses since Automated Guided Vehicles (AGVs) were first brought to market in the 1950s. Compared to today’s standards, the technology was quite basic—the vehicles simply sensed and followed a wire buried in the floor. Over the years, the technology has advanced tremendously, with navigation and safety features similar to those found in modern automobiles. In many ways, the future of autonomous vehicles has already been here with AGVs.
How AGVs and AMRs Work with Humans in Fulfillment Centers and Warehouses
In food & beverage warehouses and fulfillment centers, typical AGV systems provide transportation, perform block stacking and store and retrieve pallets from racking. Wires in the floor have been replaced by inertial (gyroscopic) navigation and laser guidance, using rotating lasers and fixed reflectors to triangulate positions and movement of the vehicle. Guide paths have become virtual and can be changed quickly and wirelessly by a computer. However, the paths for these technologies are still fixed.
But as the technology for navigation and safety has continued to improve, a whole new subset of AGVs have recently come to market. Autonomous Mobile Robotics (AMRs) are generally smaller, more nimble AGVs that take full advantage of the latest technology to perform more sophisticated work. There are many forms and price points, but AMRs typically include lasers to scan natural environments, QR Code scanning to detect location, 2D and 3D cameras or a combination of these strategies using ultrasound.
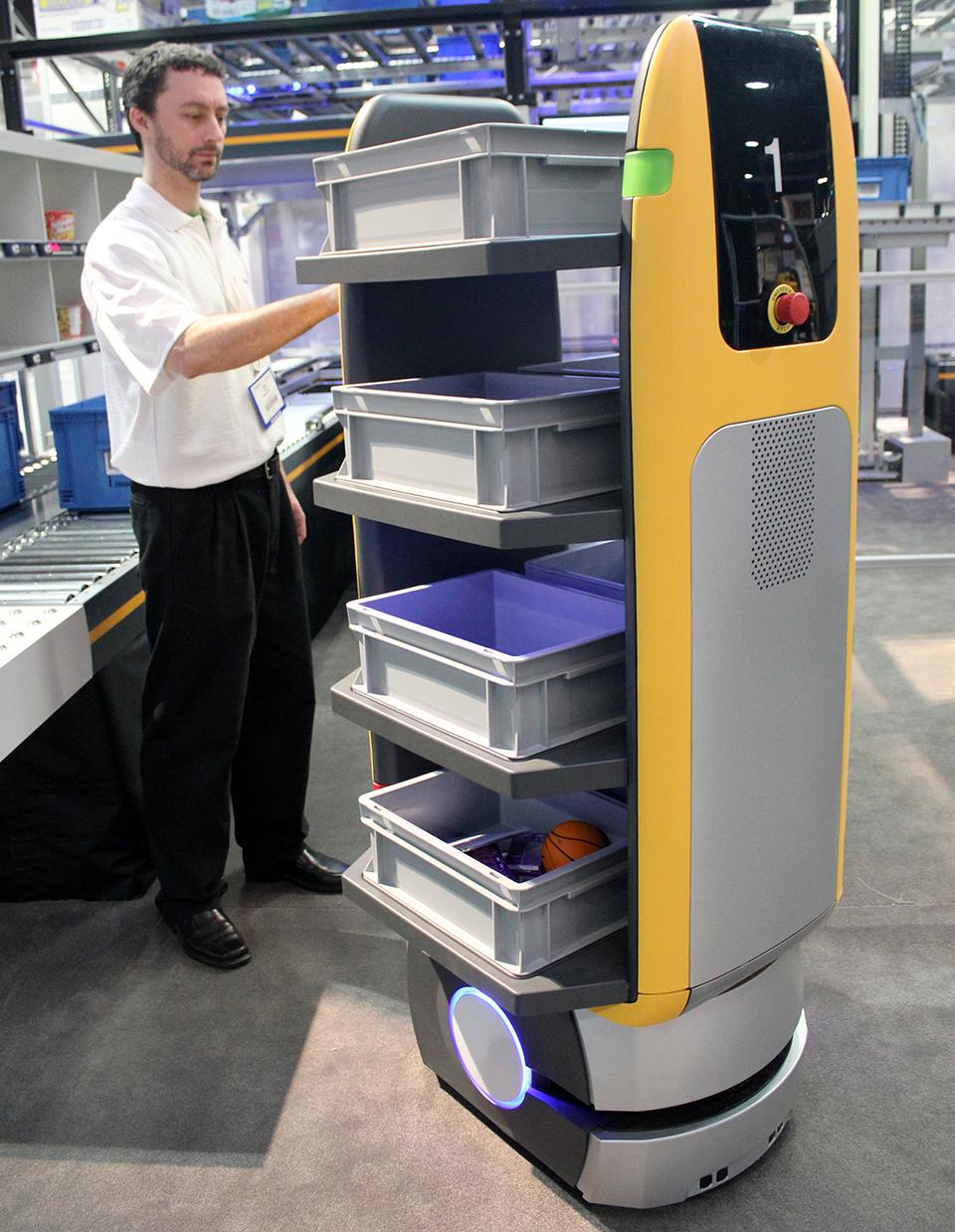
Autonomous Mobile Robotics (AMRs) take full advantage of the latest technology to perform … [+]
Dematic
As a result, AMRs can make intelligent decisions to move to different routes or move around obstacles, whereas with older technology, vehicles would wait for the path to be cleared. AMRs are already being employed in general merchandise, apparel and parcel centers. Food & beverage facilities may be the next big market.
For example, in most grocery warehouses, pallet-jacks are used by operators to move pallets. The pallet jacks can be manual or powered, but operators must still do the moving to transfer materials. This is an area ripe for automation, where AMRs replace pallet jacks to move materials from position to position, freeing operators for safer, less repetitive work.
AMRs can “lead” operators to next locations where operators pick orders and load them on the AMRs. AMRs can also follow operators as they move about the warehouse picking orders. Smaller AMRs mounted with carts or multiple totes can pick individual items or be receptacles for orders in batch picking.
Another opportunity is shelf-to-person technology in which individual items and cases are stored on shelfing units very densely packed in a warehouse. AMRs move under these shelf units, lift them slightly off the floor and move the unit to an operator pick station. This eliminates operator travel completely. Again, specific store orders can be picked at a station or a batch method could be used.
Safety is another reason why companies have turned to AGV and AMR systems. The US Bureau of Labor Statistics states that from 2011 to 2017, 614 workers lost their lives in forklift related incidents and more than 7,000 nonfatal injuries with days away from work occurred every year. Conversely, according to the Material Handling Institute (MHI), no known official records are kept on AGV injuries due to the low incident rate.
A Technology on a High-Growth Trajectory
The majority of AGV and AMR systems to date have been deployed in manufacturing environments. However, the use of the technology in logistics is estimated to surpass manufacturing in 2022 and will almost double the number of use cases in manufacturing by 2024.
To give you a sense of the growth, in 2020 it is estimated that revenue for AGVs/AMRs in manufacturing is $1.4B and in logistics is $900M. By 2024, those numbers will increase by over 70% and 90% respectively. That growth in logistics is remarkable for such a short period of time. And while implementation in general merchandise will certainly be significant, AGV and AMR usage in food & beverage and in grocery operations are expected to be higher.
As you walk through a store in the not so distant future, you may see AMRs taking shelf inventory or cleaning floors and disinfecting operations—or in a warehouse autonomously scurrying about, sorting and packing goods. And as you get in your not yet self-driving Tesla
TSLA